Global Battery Manufacturer Implements a Campus-Wide Modernization to Provide Improved Performance, Uptime and Availability of its IT Network
Objective
This manufacturer needed a networking environment that could keep pace with its growth and the adoption of the latest manufacturing technologies.
Solution at a Glance
Arraya designed a state-of-the-art manufacturing campus network based on the Cisco Connected Manufacturing reference architecture.
Challenge
The client in this case study is one of the world’s leading battery manufacturers with over 8,000 employees, 450 product designs and hundreds of awards for manufacturing and environmental excellence.
Growth has become the norm for this manufacturer. As business has grown, so has interest in incorporating the latest in manufacturing technology, including
automation, Internet of Things (loT) connected switches and sensors. More and more manufacturers see the efficiencies gained and data generated by these tools as success-drivers, and this manufacturer is no different.
As new solutions were rolled out, there was one unintended consequence. It was found that their existing networking infrastructure was struggling to keep up with the added workload. This presented the very real — and potentially expensive —problem of unplanned network and production downtime. Meanwhile, the newly-connected devices and the data they produced needed to be secured, or else they could turn into a cybersecurity liability for the manufacturer.
At the same time, the business hadn’t stopped growing. In fact, the manufacturer was planning to add a new facility to its campus, which already included 15 other sites. The idea was to position this new plant on the cutting edge of the manufacturing technology landscape.
Before that could happen, the manufacturer needed to be sure it had the technology in place to support its existing environment and to account for upcoming and future physical expansions and technological advances.
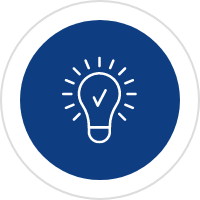
As this manufacturer grew and implemented new technology solutions, their existing network infrastructure was struggling to keep up.
Solution
The manufacturer engaged with Arraya Solutions to help architect a solution. In order to do that, Arraya first wanted to gain more insight into its technology environment from those who know it best.
Meetings were held with more than a dozen line of business groups — including facilities, safety, IT — and members of the manufacturer’s leadership team, to discuss strategy, requirements, and deficiencies. The goal was to discover what each was doing from a technology perspective — and what they would like to do if they had the technology to support it.
These findings became the basis of a Customer Requirements Description (CRD) document. Arraya then performed an assessment of the manufacturer’s infrastructure to build a GAP analysis of the manufacturer’s existing environment against the requirements stated in the CRD. This confirmed an upgrade was a must to ensure its environment was capable of addressing its growing needs. Additionally, upgrading would bring much-needed redundancy to the manufacturer’s system, ensuring operational continuity in the event of an outage.
With that information in hand, Arraya designed a state of the art manufacturing campus network based on the Cisco Connected Manufacturing reference architecture. This end-to-end structural design — which was developed by Cisco in conjunction with Rockwell Automation — is comprised of proven designs, technologies, abilities, and services. It’s intended to increase security through greater network control, enabling the quick and safe deployment of efficiency-boosting automation and ensuring uptime by enhancing the organization’s ability to spot and correct issues, among other advantages.
This architecture was designed to support the new plant, but that wasn’t all. Arraya conceived it as a framework that could be retrofitted across the manufacturer’s existing plants, providing campus-wide modernization.
The entire process would be split into at least two phases. Phase 1 involved rebuilding the manufacturer’s campus core network and instilling modern networking capabilities within its newest facility. Overlaid over top of that was deploying some initial security provisions.
During Phase 2, the architectural techniques employed during Phase 1 would be replicated throughout the rest of its campus. Bringing the manufacturer’s other facilities up to the new standard would take place over several years.
Possible future phases include layering on additional security, deploying this architecture at other planned expansions, and broadening the analytical and business dashboard capabilities available through it.
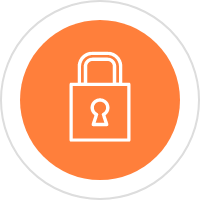
Phase 1 involved rebuilding the manufacturer’s campus core network and instilling modern network capabilities, while Phase 2 involved replicating these efforts throughout each of the manufacturer’s facilities.
Results
Upon completion, the “network as a utility” infrastructure created by the initial phases should support the customer’s operations for the better part of the next decade. As a result, the manufacturer can expect to see organization-wide improvements in the performance, uptime, and availability of its IT network across its campus. It will also be better positioned to continue to augment its processes with the latest technologies, e.g., automation. All of this will be accomplished with a greater emphasis placed on securing the organization against cyberattacks.
Those benefits — the uptime, availability, and performance — factor in to one of the company’s core performance metrics: Operational Equipment Efficiency (OEE).
Improved OEE has been a standing focus of internal enhancement initiatives at the manufacturer, much like it has been across the industry, for some time. This project will create a self-healing, highly-resilient network foundation for sparking immediate and long-term OEE improvements.
We’ve worked hard to give our diverse customer base customized IT solutions. How can we help you?
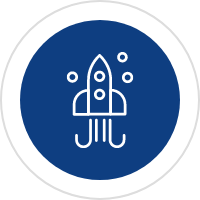
This client can now rely on a highly-resilient network foundation for sparking immediate and long-term operational efficiencies.